
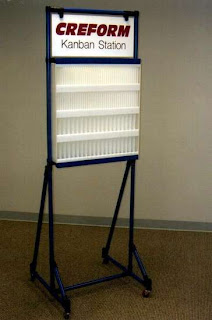
Companies and businesses all want the same thing. Profit is everyone’s main aim; however, products and goods are known for their valuable price and quality as well. Corporations and businesses need predictions in order to know their future markets. Predictions will help businesses evaluate expenses, costs, and quantities of products needed to be produced. The ability to predict future changes through research and previous market plans is indeed rare and hard to make it as a habit. Managers often fail to predict future market groups due to the lack of interest in researches and data-based information. Instead, managers often focus on current situations and current markets, striving to make profits and balance daily operations and costs. Business agility is also one of the most difficult things to accomplish. Agility involves speed, coordination, and adaptation under a single roof. Indeed with the Kanban system, things will get easier and convenience. To work under one umbrella will need a lot of cooperation from teammates. As a pull system, Kanban requires teamwork from groups of employees and it involves the capacity to handle things. Under a knowledge work, however, it is quite challenging and difficult indeed to look search for one’s capability or ability because knowledge work is invisible and highly variable. Most of the time, people often work all at the same time in knowledge work form which is also called “Multi-tasking”. In Kanban, the WIP limit or ‘Work in Progress’ concept helps reduce one’s tasks to be able to see their ability and capability. The WIP concept will visualize and make one’s capability visible through the reduction of jobs but an increase in work hours at one or two work positions. If WIP is balanced and limited, the results can be extremely surprising.
How Tasks Are Done Faster Than Normal
With the Kanban system and its WIP concept, tasks can be done easily within quite a short period of time. However, products and goods are still in a moderate to high quality. Since technology and human brains work differently, it is obvious indeed that mechanical tools work a lot better than humans do. Without WIP limits, people waste their time changing their tasks from one to another, wasting all the time needed to finish work and tasks on time. Tasks delays will most likely increase rapidly and might contribute to further losses of efficiency, reliability, and the ability to produce high quality products and services. Since everyone will work on limited specific tasks assigned by managers where some finish all tasks on time and others get easily overloaded, bottlenecks are visible. With WIP reduced, other members or workers that finished their tasks on time can help those who are extremely overloaded with tasks undone. Better yet, these people can also come up with ideas and reliable strategies to solve problems and fix newly discovered bottlenecks.

As a pull system, the Kanban system requires hard work and high cooperation from everyone in order to accomplish good results and evaluate positive performances. This system teaches businesses to control and manage their employees and workers efficiently so that goods and products are produced with care. A discovery of a team’s capacity will also lead to further positions and new ideas that can make improvements for businesses in the future. After Kanban was used, businesses can enjoy and feel convenient with a better and a sustainable team of workers that will enhance fine performances and quality. As explained previously, Kanban eliminate wastes and scraps just as the JIT does. It provides flexibility in how production lines are used and reduce costs and expenses by spending lesser on over production, developing flexible work stations, minimizing wait time and logistic costs, and reducing inventory costs or costs of keeping stocks.